Nuovo asfalto con grafene, plastiche recuperate e fresato riciclato
Rondissone (To), 20 ott. (askanews) – Un asfalto innovativo, sostenibile, resiliente e sicuro per il tratto autostradale A4 Torino – Milano, gestito dal Gruppo ASTM: sara’ realizzato con grafene e plastiche dure riciclate appositamente selezionate (come, ad esempio, giocattoli, cassette della frutta, cestini) e con il reimpiego del 70% di fresato proveniente dalla pavimentazione esistente, riducendo cosi’ al solo 30% l’utilizzo di nuovi aggregati naturali. I lavori interesseranno entrambe le direzioni di marcia per un totale di 250 km. Il Gruppo ASTM, secondo operatore al mondo di reti autostradali in concessione e player globale nella realizzazione di grandi opere infrastrutturali, impieghera’ Gipave, una tecnologia per asfalti che utilizza un processo brevettato e innovativo completamente made in Italy, risultato di una ricerca durata sei anni, condotta da Iterchimica – azienda italiana che opera in oltre 90 Paesi, leader nella produzione e messa a punto di prodotti e tecnologie per asfalti sostenibili – in collaborazione con G.Eco (gruppo A2A), Universita’ degli Studi di Milano-Bicocca e Directa Plus.
L’attivita’ di ripavimentazione rendera’ l’autostrada A4 la prima in Europa ad utilizzare un asfalto green e hi-tech grazie all’impiego del grafene e del 70% di asfalto riciclato. Un’attivita’ che si inserisce all’interno del piu’ ampio progetto “Smart Roads” del Gruppo ASTM. La tratta Torino-Milano, infatti, che collega i due principali poli economici e industriali del nord ovest del Paese, e’ stata scelta dal Gruppo per rappresentare non solo simbolicamente, ma anche di fatto, la visione ASTM dell’Autostrada del Futuro. Lungo i 125 km della tratta verranno implementate molte soluzioni innovative con lo scopo di incrementare i livelli di sicurezza, migliorare la qualita’ del viaggio degli utenti e tutelare l’ambiente.
L’impiego della tecnologia green e hi-tech Gipave e di asfalto riciclato al 70% garantisce maggiori prestazioni in termini di sostenibilita’ e resistenza, sino ad incrementare fino al 75% la durata della pavimentazione rispetto alle migliori tecnologie attualmente utilizzate sul mercato. Per raggiungere questo obiettivo il Gruppo ASTM installera’ un apposito impianto di produzione in posizione mediana rispetto al tratto autostradale A4 per gestire al meglio l’intero processo.
Rispetto ad una manutenzione standard, questa soluzione permettera’ di ridurre i consumi energetici di circa 90 milioni di kWh (-30%), corrispondenti al fabbisogno annuale di circa 30 mila famiglie e consentira’ l’abbattimento di 18.350.000 kg di emissioni di CO2eq (il 38,5% in meno) pari all’azione di assorbimento di circa 115.000 alberi. Inoltre, rispetto ad una pavimentazione realizzata con metodologia tradizionale, per questa attivita’ verranno riutilizzati circa 1,5 milioni di kg di plastiche dure (pari circa al peso di oltre 1.200 automobili), risparmiando quasi 23 milioni di kg di bitume e circa 480 milioni di kg di materie prime estratte da cave (-40% di materiali non rinnovabili impiegati rispetto alle tecnologie tradizionali).
Un’autostrada green e hi-tech: via alla ripavimentazione dell’A4
Rondissone (To), 20 ott. (askanews) – Un asfalto innovativo, sostenibile, resiliente e sicuro per il tratto autostradale A4 Torino – Milano, gestito dal Gruppo ASTM: sara’ realizzato con grafene e plastiche dure riciclate appositamente selezionate (come, ad esempio, giocattoli, cassette della frutta, cestini) e con il reimpiego del 70% di fresato proveniente dalla pavimentazione esistente, riducendo cosi’ al solo 30% l’utilizzo di nuovi aggregati naturali. I lavori interesseranno entrambe le direzioni di marcia per un totale di 250 km. Il Gruppo ASTM, secondo operatore al mondo di reti autostradali in concessione e player globale nella realizzazione di grandi opere infrastrutturali, impieghera’ Gipave, una tecnologia per asfalti che utilizza un processo brevettato e innovativo completamente made in Italy, risultato di una ricerca durata sei anni, condotta da Iterchimica – azienda italiana che opera in oltre 90 Paesi, leader nella produzione e messa a punto di prodotti e tecnologie per asfalti sostenibili – in collaborazione con G.Eco (gruppo A2A), Universita’ degli Studi di Milano-Bicocca e Directa Plus.
L’attivita’ di ripavimentazione rendera’ l’autostrada A4 la prima in Europa ad utilizzare un asfalto green e hi-tech grazie all’impiego del grafene e del 70% di asfalto riciclato. Un’attivita’ che si inserisce all’interno del piu’ ampio progetto “Smart Roads” del Gruppo ASTM. La tratta Torino-Milano, infatti, che collega i due principali poli economici e industriali del nord ovest del Paese, e’ stata scelta dal Gruppo per rappresentare non solo simbolicamente, ma anche di fatto, la visione ASTM dell’Autostrada del Futuro. Lungo i 125 km della tratta verranno implementate molte soluzioni innovative con lo scopo di incrementare i livelli di sicurezza, migliorare la qualita’ del viaggio degli utenti e tutelare l’ambiente.
L’impiego della tecnologia green e hi-tech Gipave e di asfalto riciclato al 70% garantisce maggiori prestazioni in termini di sostenibilita’ e resistenza, sino ad incrementare fino al 75% la durata della pavimentazione rispetto alle migliori tecnologie attualmente utilizzate sul mercato. Per raggiungere questo obiettivo il Gruppo ASTM installera’ un apposito impianto di produzione in posizione mediana rispetto al tratto autostradale A4 per gestire al meglio l’intero processo.
Rispetto ad una manutenzione standard, questa soluzione permettera’ di ridurre i consumi energetici di circa 90 milioni di kWh (-30%), corrispondenti al fabbisogno annuale di circa 30 mila famiglie e consentira’ l’abbattimento di 18.350.000 kg di emissioni di CO2eq (il 38,5% in meno) pari all’azione di assorbimento di circa 115.000 alberi. Inoltre, rispetto ad una pavimentazione realizzata con metodologia tradizionale, per questa attivita’ verranno riutilizzati circa 1,5 milioni di kg di plastiche dure (pari circa al peso di oltre 1.200 automobili), risparmiando quasi 23 milioni di kg di bitume e circa 480 milioni di kg di materie prime estratte da cave (-40% di materiali non rinnovabili impiegati rispetto alle tecnologie tradizionali).
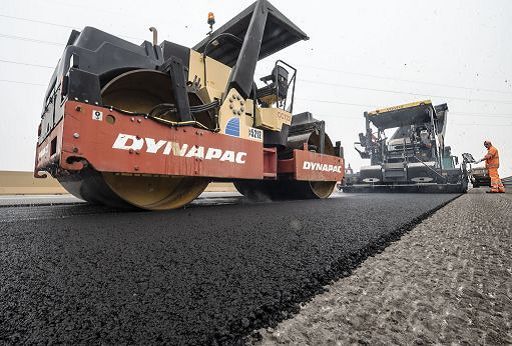